右の画像はボルトとナットの断面ですが、意外と隙間が多く、実際に接触しているのは10~20%程度です。
ボルトとナットの表面に付着したダスト・水分等によりスレッド部分に錆が発生し、隙間を埋めてしまう事で、溶着してしまい分解時にボルトが回らなくなる現象が発生します。
一般的に錆の体積は2.5倍に膨れ上がると言われ、その発生圧力は140㎏/cm2にもなります。
ボルトとナットの焼き付きの原因は腐食と摩擦です
多く原因は錆による固着
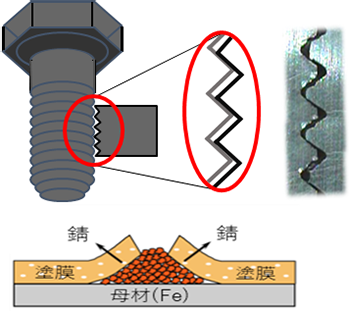
錆の発生要因は酸素と水
屋外の機器・屋内でも湿度の高い雰囲気にあるボルトは酸化して、腐食が発生します。そのため、焼付防止剤には潤滑性能と共に耐水性や耐腐食性が重要な要素となります。
ステンレスのボルトは注意
ステンレス製のボルトは薬品環境など耐腐食性が求められる環境で使用されますが、錆びない代わりにガジリが発生しやすいボルトになります。
鉄鋼と比較して摩擦係数が高く、熱伝導性が低く、熱膨張係数が2倍あります。
強いトルクで締めると溶着しやすい為、分解時に外れないケースが多く、締付時の潤滑とトルク管理が重要になってきます。
ボルトの潤滑剤を塗布してますか
ボルトを締結する際に塗布する焼付防止剤は大切な潤滑剤の役割を果たします。
金属同士が無潤滑で接触すれば、高い摩擦が発生し、焼き付き(がじり)が発生します。
たとえて言うなら、ベアリングを無潤滑で使用する様なものです。
適切なボルト締結作業には焼付防止剤の潤滑が欠かせません。
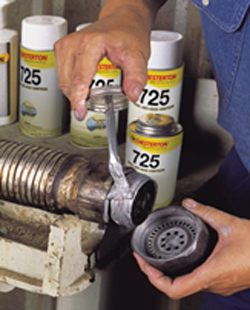
トルク管理に潤滑度は重要です
焼付防止剤が有りと無しでは、かけたトルクと実際にかかる軸力に大きなバラつきがでます。では焼付防止剤の種類によっても差が出ることはご存じでしょうか?
ボルト締結に際して、トルク管理を行われている方も多いと思いますが、その際には適切なナット係数が重要となります。簡単にいいますと、摩擦が高すぎるのだめですが、摩擦が低すぎるのもよくないという事です。
摩擦が高いと、トルクレンチよりも実際のトルクは低くなり、逆によく滑る場合は強く締まってしまう傾向となります。
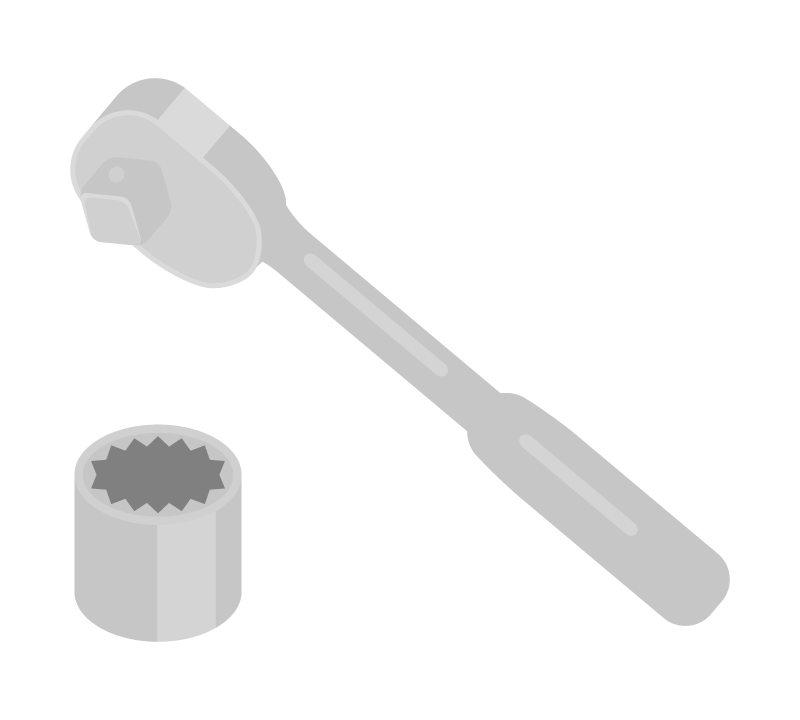
焼付防止剤を選ぶポイント
1. 腐食(錆)に対して高い耐性
ボルトの腐食に対してどれだけ防食効果・錆の発生を抑えるかこれはボルトナットの内部だけでなく、外部突出部の腐食防止も重要です。
2.水に洗い流されない耐水性
屋外の機器に塗布した焼付防止剤が、雨・潮風にさらされ、流されると腐食の原因となります。耐水性能が高い製品を選びましょう。
3.高温下でも機能する耐熱性
熱によって基油は蒸発しますが、残った微細粒子が金属表面に被膜を張り、スムーズな分解に貢献します。
4.局所的荷重に耐える極圧耐性
ボルト締結・分解時にかかる極圧に耐え、ガジリを起こしずらいかが重要。
焼付防止剤が微細粒子であり、かつ均一な粒子径で作られている製品が推奨されます。
5.安定した摩擦係数
ナット係数のばらつきが大きい焼付防止剤の使用は、トルク管理における信頼性の低下とフランジシールの品質低下を招きます。
ボルトナットの締結・分解は工場内作業の大部分を占めています。
全ての締結・分解作業がスムーズにいけば、コストの削減はもちろん、交換に費やす作業時間の短縮に多大なる貢献が見込まれます。
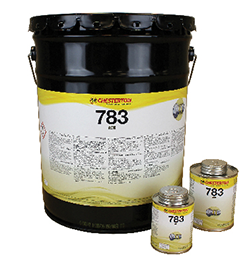
【お試しください】
#783 ACR焼付防止剤
特長
- 非常に優れた耐水性、水で流されない
- 非常に優れた極圧耐性
- 不活性型腐食抑制剤入り (塩霧腐食テスト1000時間以上)
- 酸雰囲気での優れた耐性
- 安定したナット係数
- 重金属を含まない
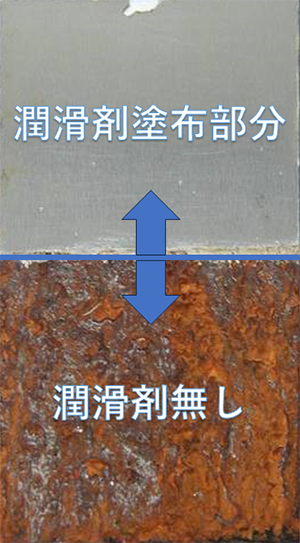
塩霧腐食テストピース